
Understanding Custom-Built Bearings
Custom-built bearings are specialized components designed to meet the specific requirements of individual applications where standard bearings might not suffice. Unlike off-the-shelf options, these tailored solutions offer enhanced performance, longevity, and efficiency by addressing unique operational challenges.
Standard bearings can often fall short in scenarios requiring unique dimensions, unusual load capacities, or exposure to extreme environmental conditions. In such cases, custom-built bearings become indispensable to achieve optimal functionality.
Industries like aerospace, medical devices, automotive, and heavy machinery frequently benefit from custom solutions due to their stringent demands and application-specific needs. The ability to customize every aspect of a bearing ensures that it meets precise criteria, thus enhancing overall productivity and reliability.
The Design Process
The journey towards a perfect custom-bearing solution begins with an initial consultation. Understanding specific needs is paramount during requirement gathering. Key questions revolve around operational demands, environmental factors, and performance expectations, ensuring no detail is overlooked.
The engineering and design phase involves close collaboration between engineers and clients. Utilizing advanced software tools, precision designs are crafted to match the customer's exact specifications. This collaborative effort guarantees that the final product will perform as intended under real-world conditions.
Creating prototypes plays a crucial role in this process. Prototypes are meticulously tested to validate design accuracy and functional performance. Rigorous testing processes ensure that durability and reliability are built into each custom bearing right from the start.
Material Selection
Selecting the right materials significantly impacts the bearing’s performance and lifespan. Commonly used materials include metals such as stainless steel and titanium, alongside composites and ceramics. Each material offers distinct advantages regarding strength, weight, and resistance properties.
Factors influencing material choice involve evaluating load capacity, environmental conditions including temperature extremes, humidity levels, and chemical exposures. These considerations help determine which materials best suit the application's specific requirements.
Manufacturing Techniques
Specialized manufacturing processes bring custom bearings to life. CNC machining allows for high precision in shaping complex geometries, while additive manufacturing (3D printing) offers flexibility in prototyping and low-volume production runs. Heat treatment and surface finishing techniques further enhance the mechanical properties and surface quality of the bearings.
Ensuring top-notch quality throughout the manufacturing process is vital. Precision measurement tools and techniques are employed to maintain consistency and adherence to specifications. Robust quality control measures guarantee that each bearing delivers consistent and reliable performance.
Benefits of Custom-Built Bearings
Opting for custom-built bearings provides several benefits, including enhanced performance and greater longevity, reducing downtime and maintenance costs. Their bespoke nature translates into improved efficiency and productivity by catering to specific operational environments and conditions.
Real-world Applications
In the aerospace industry, precision and reliability are non-negotiable, making custom-built bearings essential. Medical devices require customized bearings to ensure safety and precision during operations. Automotive industries leverage tailor-made solutions for better vehicle performance, and heavy machinery relies on durable bearings to withstand strenuous workloads.
Success stories abound across various sectors, showcasing how custom-built bearings have revolutionized operational efficiency and dependability. Testimonials from satisfied clients affirm the transformative impact of these specialized solutions.
Cost Considerations
While the initial investment in custom-built bearings might be higher than standard ones, long-term benefits far outweigh the costs. Reduced failures and lower maintenance expenses lead to significant cost savings over time. Moreover, financing and support options make the acquisition process viable.
Future Trends and Innovations
Emerging technologies promise exciting advancements in custom bearing design. Smart bearings equipped with embedded sensors provide real-time data for predictive maintenance. Advanced materials and coatings continue to push the boundaries of performance.
Artificial Intelligence and machine learning play increasingly crucial roles in optimizing design and manufacturing processes, paving the way for more efficient and effective custom solutions.
How to Get Started
Selecting the right provider for custom-built bearings involves careful consideration of key criteria such as experience, technical expertise, and customer service. Asking potential vendors pertinent questions helps in making informed decisions.
Ongoing support and service are integral to maximizing the value of custom solutions. Providers offering comprehensive maintenance, upgrade options, training, and documentation add considerable value to their offerings.
Additional Resources
For those interested in further exploring the world of custom-built bearings, recommended readings include technical papers and industry publications. Engaging in forums and joining professional associations provide valuable insights and networking opportunities. Contact us at Xin Hongchang for expert consultations and inquiries about our premium bearing solutions.
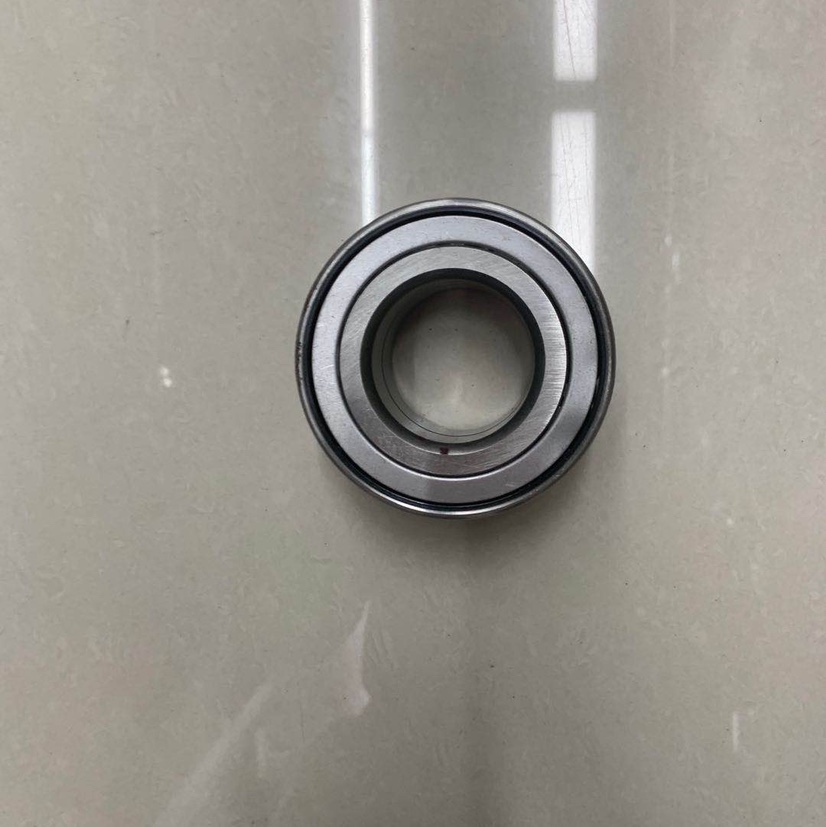